xingkong星空体育:先进制造技术-5-6微机械及微细加工技术
文章出处:本站 人气:发表时间:2024-01-18 13:58
1、五、微机械及微细加工技术1、微机械简介现代制造技术的发展有两大趋势:一是向着自动化、柔性化、集成化、智能化等方向发展,使现代制造成为一个系统,即现代制造系统的自动化技术。另一个就是寻求固有制造技术的自身微细加工极限。探索有效实用的微细加工技术,并使其能在工业生产中得到应用。微机械由于具有能够在狭小空间内进行作业而又不扰乱工作环境和对象的特点,在航空航天、精密仪器、生物医疗等领域有着广阔的应用潜力,受到世界各国的高度重视并被列为21世纪的关键技术之首。比如,美国宇航局投资1亿美元着手研制“发现号微型卫星”;说明:卫星有大型、小型卫星、微型卫星和纳米卫星,区别是:小型卫星为一种可用常规运载器发射的
2、航天器,质量为100500kg;微型卫星定义为所有的系统和子系统都全面体现了微型制造技术,质量为10100kg;纳米卫星是一种尺寸减小到最低限度的微卫星,质量为110 kg。在航天发展史上,由于受运载能力及技术水平的限制,早期研制的卫星都采用小卫星方案,其重量只有几十千克。70年代末,由于大推力运载火箭的研制成功和设计与制造能力的提高,大型多功能卫星开始出现,卫星体积不断增大,功能也越来越复杂。随之而来的是成本不断攀升,风险逐渐增加。如一枚“大力神”“半人马座”运载火箭连同所发射的侦察卫星价值可达10.5亿美元以上,一旦发射失败就会造成严重的损失。而且,卫星一旦被淘汰,形成严重的太空污染。为此
3、,航天界又将目光重新投向了小卫星。由于技术的进步,特别是微电子技术的进步,新一代的小卫星采用了许多小型高性能电子部件,但它们同样具有一些大型卫星才有的功能,并为小卫星进一步微型化,进而为微型卫星、纳米卫星的发展奠定了基础。纳米卫星的概念最早是由美国宇航公司于1993年在一份研究报告中首次提出的,它带来了小卫星设计思想上的根本变革。纳米卫星是以微机电一体化系统(MEMS)技术和由数个MEMS组成的专用集成微型仪器(ASIM)为基础的一种全新概念的卫星,重量在10千克以下,甚至可降低到0.1千克以下。微小型卫星具有研制周期短、更新换代快、造价低、能快速发射等诸多优点,特别适用于在局部战争中的战区通
4、信和对战区进行短期侦察、监视和跟踪等。面对未来局部战争时间上的突发性、战争爆发地点的不确定性和战场瞬息万变等情况,这些都需要战场指挥员根据具体要求应急发射小卫星,并在2472小时内完成部署。目前的纳米卫星大多还处于演示和试验阶段,一旦真正投入实际应用以后,由于其技术已经成熟,卫星生产成本将降低,并且由于其重量轻、体积小,可一箭多星发射,发射成本也将大大低于一般卫星。另外,卫星的研制将不再需要大型的试验设施和厂房,可以在大学或研究所的实验室里研制,研制费用也大大降低。研制、生产和发射成本的降低,将促进其商业化。1、1 微机械的特点微机械之所以受到人们的关注,是因为它具有诱人的特点:(1)体积小、
5、重量轻、精度高。其体积可小至亚微米以下(小于20微米,人眼已不能分辨),重量可轻至纳克,尺寸精度可高达纳米级。已经制出了直径细如发丝(头发丝的直径约0.07mm)的齿轮、能开动的3mm大小的汽车和花生米大小的飞机。注:蚂蚁腿上的齿轮:蚂蚁身长约3.6毫米,腿的直径约0.16毫米(2)性能稳定、可靠性高。由于微机械器件的体积极小,几乎不受热膨胀、噪声及挠曲变形等因素的影响,因此具有较高的抗干扰能力,可在较差的工作环境下稳定地工作。(3)能耗小、响应快、灵敏度高。完成相同的工作,微机械所消耗的能量仅为传统机械的十几分之一或几十分之一,而运作速度却可达其10倍以上。如微型泵的体积可以做到(5mm5m
6、m07mm),远小于小型泵,但其流速却可达到小型泵的1000倍。由于机电一体的微机械不存在信号延迟等问题,因此更适合高速工作。(4)多功能化和智能化,既能感知环境又能控制环境。许多微机械集传感器、执行器和电子控制电路等为一体,特别是应用智能材料和智能结构后,更利于实现微机械的多功能和智能化。(5)适于大批量生产,制造成本低廉。微机械能够采用与半导体制造工艺类似的生产方法,像超大规模集成电路芯片一样,一次制成大量完全相同的零部件,因而可大幅度降低制造成本。如美国的研究人员正在用该技术制造双向光纤通信所必须的微型光学调制器。通过巧妙的光刻技术制造芯片,做一块芯片只需几美分,而过去则要花5000美元
7、。1、2 微机械的优势从功用上看,微机械具有以下一般机械所不能及的优势:(1)首先表现在活动空间、操作对象和工作环境上。微机械能够进入极狭小的空间进行作业,且不易对环境造成不必要的影响与破坏。在医学上,微机械可游弋于人体血管,去清除血栓或其它病理组织;在工程上,可以进入精密机械或仪器内部进行故障检修或其它操作。微机械还可以面对很脆弱、易损伤的工作对象,例如接通大脑中的细微神经、检修微型或超微型计算机中的通讯光纤等。此外,微机械还可出现于人类所不能及或不适宜的工作环境,如清洁长期运行于宇宙空间的卫星摄像机镜头、在有核辐射的场所执行任务等。(2)与一般机械相比,微机械所表现出的智能化程度更高、实现
8、的功能更趋于多样化。由于微机械的工作环境比较复杂,除了人类必备的控制以外,微机械自身也须具有一定程度上的自主分析、判断和处理特定事件的能力。在需要多个微机械共同去完成任务时,相互之间的分工和协作也是必需的。这都要求微机械具有较高的“智能”。采用新型材料和新方法制作的微机械可以不同于传统机械,它能将驱动与执行等多项功能集中于同一构件,使整体结构简单、尺寸更易微小化。1、3 微机械的研究开发内容(1)理论基础当尺寸缩小至一定范围时,许多物理现象与宏观世界有很大差别。在微观尺寸领域,与尺寸L的高次方成比例的惯性力、电磁力(L3)等的作用相对减小,而与尺寸的低次方成比例的弹性力(L2)、表面张力(L1
9、)、静电力等的作用相对增大,同时表而积(L2)与体积(L3)之比增大,热传导、化学反应加速和表面间的摩擦力显著增大。因此,许多宏观物理量进入微观尺度后甚至需要重新定义。相关学科,如微电子学、微机械学、微光学、微动力学、微流体力学、微热力学、微摩擦学、微结构学和微生物学等共同构成了微机械研究的理论基础。(2)技术基础 基本技术包括:微机械设计、微机械材料、微细加工、微装配与封装、集成技术、微测量等。(3)应用研究 美、日、德等国在微机械的研究与应用方面占据领先地位。美国很早就着手微机械的研究,尤其是斯坦福大学,在20世纪60年代便利用硅片腐蚀方法制造了应用于医学的脑电极阵列的探针,后来又在微型传
10、感器等方面取得成功。例如:参考书164日本在此领域的研究虽然起步晚于美国,但目前注重程度和投资强度均超过美国。日本通产省1991年开始启动一项为期10年、耗资250亿日元的微型机械大型研究计划,研制两台样机,一台用于医疗,进入人体进行诊断和微型手术;另一台用于工业,对飞机发动机和原子能设备的微小裂纹实施维修。日本政府还投资3千万美元:至建了一座新的“微型机器人中心”。 日本名古屋大学研制了直径为6mm、具有16个爪的管道流通微机器人。德国在微细加工方面首创了LIGA(德语制版术、电铸成形、注塑三个词的缩写)工艺,即X光深度光刻、微电铸和微塑铸三种工艺的有机结合,可实现高深宽比的微结构制作。例如
11、LIGA工艺制作出直径80 um、厚度140 um的微齿轮,可用于微机械的动力传输。用LIGA技术制造的微加速器,可用于汽车安全气囊的控制系统。安全气囊作用原理:安全气囊只能在乘客和方向盘或仪表板之间的有限空间内发挥作用,并且必须在几分之一秒的时间内完成使命。气囊自身由纤细的尼龙纤维制成,折叠后装入方向盘或仪表盘。近来还出现了装入座椅或车门的气囊。 在撞击的瞬间,传感器是通知气囊充气的设备。传感器从内置于微芯片中的加速计接收信号(即LIGA微加速度传感器)。 只要所测加速度超过了安全值,点火器就被点着,安全气囊充气系统中的叠氮化钠(NaN3)和硝酸钾(KNO3)发(“固体推进剂”)就会发生反应
12、,生成氮气,这个原理与固体火箭助推器的原理相同。大量的氮气形成的热流会让气囊迅速膨胀。随后,气囊爆炸般地冲出原始安装位置,时速高达322公里,比眨一下眼睛还要快!整个过程只经历短短的1/25秒,但多出的这点时间已足以防止人员遭受重创。1秒之后,气体通过气囊上的小孔迅速消散,气囊收缩,因此乘客又可以自由移动。2.微细加工技术微细加工技术包含了各种传统精密加工方法和与其原理截然不同的新方法,如微细切削加工、磨料加工、微细电火花加工、电解加工、化学加工、超声波加工、微波加工、等离子体加工、外延生长、激光加工、电子束加工、离子束加工、光刻加工、电铸加工等;狭义地讲,微细加工技术目前一般主要是指半导体集
13、成电路(IC)的微细制造技术,因为微细加工技术是在半导体集成电路制造技术的基础上发展起来的,如化学气相沉积、热氧化、光刻、离子束溅射、真空蒸镀、LIGA等。1987年,美国利用IC工艺首次制造出直径为100um的硅静电微型电机,转子的直径仅为60um。2、2 微细加工技术特点微机械的微细加工技术有以下特点:(1)从加工对象上看,微细加工不但加工尺度极小,而且被加工对象的整体尺寸也很微小;(2) 由于微机械对象的微小性和脆弱性,仅仅依靠控制和重复宏观的加工相对运动轨迹达到加工目的,已经很不现实。必须针对不同对象和加工要求,具体考虑不同的加工方法和手段;(3) 微细加工在加工目的、加工设备、制造环
14、境、材料选择与处理、测量方法和仪器等方面都有其特殊要求。(4)加工机理与一般加工相比,存在很大差异。由于加工单位的急剧减小,此时必须考虑晶粒在加工中的作用。假定把软钢材料毛坯切削成一根直径为0.1mm、精度为0.01mm的轴类零件。实际加工中,对于给定的要求,车刀至多只允许能产生0.01mm切屑的吃刀深度;而且在对上述零件进行最后精车时,吃刀深度要更小。由于软钢是由很多晶粒组成的,晶粒的大小一般为十几微米,这样,直径为0.1mm就意味着在整个直径上所排列的晶粒只有10个左右。如果吃刀深度小于晶粒直径时,那么,切削就不得不在晶粒内进行,这时就要把晶粒作为一个个的不连续体来进行切削。相比之下,如果
15、是加工较大尺度的零件,由于吃刀深度可以大于晶粒线度,切削不必在晶粒中进行,就可以把被加工体看成是连续体。这就导致了加工尺度在亚毫米、加工单位在数微米的加工方法与常规加工方法的微观机理的不同。另外,还可以从切削时刀具所受的阻力的大小来分析微细切削加工和常规切削加工的明显差别。实验表明,当吃刀深度在0.1mm以上进行普通车削时,单位面积上的切削阻力为(196294)Nmm2;当吃刀深度在0.05mm左右进行微细铣削加工时,单位面积上的切削阻力约为980Nmm2;当吃刀深度在1um以下进行精密磨削时,单位面积上的切削阻力将高达12740Nmm2,接近于软钢的理论剪切强度。因此,当切削单位从数微米缩小
16、到1微米以下时,刀具的尖端要承受很大的应力作用,使得单位面积上会产生很大的热量,导致刀具的尖端局部区域上升到极高的温度。这就是越是采用微小的加工单位进行切削,就越要求采用耐热性好、耐磨性强、高温硬度和高温强度都高的刀具的原因。2、3 微细加工设备制造设备的微小型化将有利于节约空间、节省能源、易于重组。日本通产工业技术院机械工程实验室(MEL)1996年开发了世界上第一台微型化的机床微型车床。其规格为:长32mm,宽25mm、高305mm,重量为100g,主轴电机额定功率1.5W,转速1000rmin。加工最小工件外圆为60um。说明:以下简介一种1999年由日本金泽大学研制的一套尺寸约200m
17、m的微细车削系统。它由微细车床、控制单元、光学显微装置和监视器组成。 (1)主体结构部分。在该系统中,采用了一套光学显微装置来观察切削状态,还配备了专用的工件装卸装置。图37为微细车床的结构示意图及其实物照片。主轴用两个微型滚动轴承支承,由直流电机带动主轴旋转,工件直径0.3mm,X、Y、Z轴的进给分辨率为4nm。因为工件的直径很小,车削时沿X-Y移动方向幅度不大,所以令刀架沿XY移动。工件装在主轴前端的微型夹头上。(2)切削刀具与刀架。图39是微刀架装置。刀轴安装在刀架上,通过微柄操作使其能够转位。对于微细车削端面、圆柱面、槽、锥形面等各种形状的加工,则可通过变换刀尖刃在空间的方向和位置,以
18、适应不同类型零件的切削工艺要求。(3)微细车削加工实例。利用上述微细车床可加工不同形状的回转体零件,如阶梯轮廓切削、端面切削、槽切削、镗孔和螺纹车削等。图311是其加工的部分实物照片。用直径为03mm的黄铜丝为毛坯,单点金刚石刀具加工。图311(a)为阶梯轮廓车削,小端长200um;(b)为车削端面,直径约100um;(c)为切槽加工,槽深约30um,长约100um;(d)为镗孔加工;(e)是该车床连续车削切出的微细轴,最小直径为10um;(f)为加工出的微细丝杠,螺距为125um,直径约120um,螺牙约为60度。1999年日本机械技术研究所设计制作了世界上第一台桌面微型工厂样机,由微型车床
19、、铣床、搬运机械手和装配用的两个手指机械手组成,占地70cmx 50cm,能进行加工和装配,并成功地试生产了外径D99um、长3mm的枢轴球轴承。为了演示和证明微型工厂的可携带性,2000年又设计制作了便携式微型工厂,由微型车床、铣床、冲压机、搬运机械手及电路、控制装置等组成,重23kg,放在380x 625 x490mm3重11kg的箱子里。箱子底都装有小轮,可以像旅行箱一样被推着走。 还有微细铣削和磨削,这里我们不再介绍。以上主要介绍的是类似传统加工手段的微细加工。更多的微机械产品(比如微压力、温度传感器、微型泵、微马达、微齿轮等等)大多都用到特种加工工艺。这些工艺主要来自大规模和超大规模
20、集成电路的加工工艺,正是借助于这些微细加工技术使众多的微电子器件及相关技术和产业蓬勃兴起,并迎来了人类社会的信息革命。同时微细加工技术也逐渐被赋予更广泛的内容和更高的要求。当然,今天微机械领域的重要角色不仅仅是微电子部分,更重要的是微机械结构或及其与微电子等的集成。只有将这些微机械结构及其与微电子等集成在一起才能实现微传感器或微致动器件,进而实现MEMS。也就是说,所以微机械的微细加工并不仅限于微电子制造技术,更重要的是指微机械构件的加工或微机械与微电子、微光学等的集成结构的制作技术。3、常用微细加工工艺3、1 集成电路的工艺基础1999年以来,电子信息取代石油、钢铁等传统产业,成为全球第一大
21、产业。发达国家经济增长的65%与集成电路相关。2001年世界集成电路市场份额,美国约占40%,日本25%,韩国12%,中国仅为2.1%。目前我国已有五、六十条芯片生产线,到2010年,IC领域上我国要占世界市场份额的5%以上。上海市是我国IC芯片线最集中、生产技术水平最高、8英寸(晶圆尺寸)线最多的城市。现代高科技战争,很大程度上打的是“芯片战”。据美国有关方面数据,军舰、战车、飞机、导弹和航天器中,所用IC占装备和武器成本的比重,分别达到22%、24%、33%、45%和66%。美国国防预算中的电子含量已占据半壁江山。可以说,作为信息产业基础的集成电路,是21世纪国家生存与发展的物质与技术基础
22、。正因为如此,世界主要国家都十分重视集成电路产业的发展,纷纷制定面向21世纪的集成电路发展规划,整合国内科技资源,成立国际科技合作组织,抢占制高点,以掌握未来信息技术的核心主动权。芯片工厂一直是高科技生产的圣地,图为其无尘、超净的工作环境。 目前,内存、微处理器和ASIC芯片(专用集成电路,是指应特定用户要求和特定电子系统的需要而设计、制造的集成电路)是半导体产业中最常制造的三种IC芯片。IC所用的材料主要是硅、锗和砷化镓等,全90%以上IC都采用硅片。集成电路制造过程共分4个阶段:单晶硅片制造前半制程硅片测试后半制程。整个过程中要应用到微细加工和超精密加工等先进制造工艺和设备。3.1.1单晶
23、硅片制造制造IC的硅片,不仅要求具有极高的平面度和极小的表面粗糙度,而且要求表面无变质层、无划伤。单晶硅片的超精密加工(包括超精密磨削、研磨和抛光)工艺和设备在IC制造过程中具有重要作用,是IC制造的关键技术。主要分为以下几个步骤:1)单晶生长由于自然界中没有单质硅的存在,我们使用的硅是从二氧化硅中提纯而来。二氧化硅广泛存在于自然界中。在硅提纯的过程中,原材料硅将被熔化,并放进一个巨大的石英熔炉。这时向熔炉里放入一颗晶种,以便硅晶体围着这颗晶种生长,直到形成一个几近完美的单晶硅,称为硅锭。2)切断:目的是切除单晶硅棒的头部、尾部及超出客户规格的部分,将单晶硅棒分段成切片设备可以处理的长度。3)
24、磨外圆 由于单晶硅棒的外径表面并不平整且直径也比最终抛光晶片所规定的直径规格大,通过外径滚磨可以获得较为精确的直径。4)切割晶圆 接下来硅锭将被切割成片状,称为晶圆。晶圆才被真正用于CPU的制造。所谓的“切割晶圆”也就是用机器从单晶硅棒上切割下一片事先确定规格的硅晶片,并将其划分成多个细小的区域,每个区域都将成为一个CPU的内核(Die)。一般来说,晶圆切得越薄,相同量的硅材料能够制造的CPU成品就越多。随着半导体工业的飞速发展,为满足现代微处理器要求,同时集成电路芯片制造厂为获取更多的利润,一方面,扩大芯片产量,降低单元制造成本,这要求硅片的直径不断增大;另一方面,通过提高IC的集成度,芯片
25、尺寸相对缩小,一片晶圆就能产生更多的芯片。这两种方式均可使集成电路芯片制造厂获取更多的利润。作为基底材料硅晶片的尺寸越来越大,已由原来的200 mm向300mm转化(即由8英寸芯片向12英寸芯片转化,12英寸芯片是全球最高端的芯片产品,被称为“芯片之王”,广泛应用于手机、计算机、数码相机等消费电子产品,目前全球只有46条生产线。世界第三大芯片制造商上海中芯国际2006年在北京建成我国第一条12英寸芯片生产线;第二条在武汉,委托中芯国际集成电路制造公司经营管理;第三条在大连,英特尔在大连投资25亿美元建立一个生产300毫米(12英寸)晶圆的工厂。这一工厂,即英特尔68号厂是英特尔在亚洲的第一个芯
26、片生产厂);而要缩小芯片尺寸,则要求硅片的刻线宽度越来越细(线宽是指芯片上的最基本功能单元门电路的宽度,因为实际上门电路之间连线的宽度同门电路的宽度相同,线宽可以描述IC制造工艺水平。缩小线宽意味着晶体管可以做得更小、更密集,可以降低芯片功耗,系统更稳定,CPU得以运行在更高的频率下)。刻线宽度:1995年为0.35m,1998年为0.25m,然后是0.18m,接着是0.13m(中芯能做0.13um的),目前先进国家工艺水平已达0.09线宽(Intel的Pentium 4芯片的线宽),硅片表面粗糙度要求达到纳米和亚纳米级,芯片集成度达到9000万个晶体管/cm2等。而我国最高水平仅0.13,差
27、距为1代。据美国半导体协会预测,2014年半导体线宽将达0.035,届时硅基芯片的微细加工技术将可能达到极限,微电子基础理论、材料和加工技术都可能发生革命性变化。或者接着先粗磨(同时磨许多晶圆)5)倒角:指将切割成的晶片锐利边修整成圆弧形,防止晶片边缘破裂及晶格缺陷产生。接下来精磨(只磨一片)6)研磨:指通过研磨除去切片和轮磨所造成的锯痕及表面损伤层(加工变质层),有效改善单晶硅片的翘曲度、平坦度与平行度,达到一个抛光过程可以处理的规格。硅片研磨加工质量直接影响到其抛光加工质量及抛光工序的整体效率,甚至影响到IC的性能。单晶硅属于硬脆材料,对其进行研磨,材料的破坏以微小破碎为主,要求研磨加工后
28、的理想表面形态是由无数微小破碎痕迹构成的均匀无光泽表面。硅片研磨时,重要的是控制裂纹的大小和均匀程度。7)腐蚀:研磨后已具有较高的面型,但表面粗糙度达不到要求,而且晶圆表面有损伤层,需要通过腐蚀。通常采用化学腐蚀去除。8)抛光:腐蚀去除的过程中腐蚀率难以控制,会影响面型精度。这是需抛光。集成电路集成水平越来越高的这种发展趋势,使得硅片表面的微小缺陷便可导致整个器件报废的后果,所以硅片的抛光就成为半导体制造加工技术上最重要的一道工序。对集成电路( IC)特别是超大规模集成电路(ULSI)影响更大。因此,抛光硅片的表面质量直接关系到器件的性能质量和成品率。目前普遍认为,对于线宽在0.35m及以下的
29、器件,必须进行全局平面化,而化学机械抛光(CMP,ChemicalMechanicalPolishing)是作为目前唯一的可以提供在整个硅片上全面平坦化的工艺技术。抛光的方式包括粗抛,主要作用是去除损伤层;精抛,主要作用是改善晶片表面的微粗糙程度。CMP,进行硅片的最终精抛光的加工方法。晶圆表面可获得极高平坦度、极小表面粗糙度值的晶片表面,表面无变质层、无划伤。3.1.2 前半制程接下来,完成集成电路的制作。以CPU为例,其所需处理步骤可达数百道,而其所需加工机台先进且昂贵,动辄数千万一台。虽然详细的处理程序是随着产品种类与所使用的技术有关;不过其基本处理步骤通常是进行氧化、光刻、刻蚀及选择性
30、扩散等步骤。来完成晶圆上电路的加工与制作。(1)氧化 硅的氧化物二氧化硅(Si02)与半导体硅的性能不同,它是良好的绝缘体。因此Si02膜在晶体管和集成电路中成为良好的防止短路的绝缘体和电容的绝缘介质(硅在常温下于空气中可以自然氧化,生长出Si02氧化层,但其层厚较薄,通常只有2nm左右。若要形成较厚的氧化膜,就需要在高温炉内进行,称为热氧化法)。此外,Si02膜还有以下两个特性:化学性质稳定且耐高温,故能适应集成电路制作过程中多次反复的高温处理;Si02膜对硼(B)、磷(P)、砷(As)等杂质元素有极好的抗拒性,使它们的原子不能侵人基片。利用Si02膜的这一特性,用光刻(蚀)方法将Si02膜
31、刻蚀成微小的几何图形,在杂质扩散时只有已被刻蚀去除Si02的反域(俗称“窗口”)才允许杂质扩散进入晶片内部,形成预定要求的一定几何形状的扩散区或PN结。Si02的这些特性被用作选择扩散和制作各种几何形状图形PN结的工艺依据。(2)光刻1958年光刻技术在半导体器件制造中首次得到成功应用,研制成平面型晶体管,从而推动了集成电路的发明和飞速发展。数十年以来,集成技术不断微小型化,其中光刻技术发挥了重要的作用。光刻分辨率越小,线宽越细,即集成度越高。1)工作母版制作a. 原图制作:按照芯片产品图纸的技术要求,采用CAD等技术对芯片复杂电路结构图样进行图形设计。在计算机完成的集成电路的电路图还只是一些
32、图像或(和)数据,在将设计结果送到工艺线上实验时,还必须经过一个重要的中间环节:制版,制作工作母版。即设计与工艺制造之间的接口是版图。b. 母版制作 然后原图数据被传送给图形发生器(一种制版设备),图形发生器(PG-pattern generator)根据数据,将设计的原图结果缩小并分层地转移到掩模版上(掩模版为涂有感光材料的优质玻璃板),从而得到工作掩膜或工作母版,这个过程叫初缩。通常一个CPU芯片包含好几层电路。所以通常有十几块掩膜。在获得分层的初缩版后,再通过分步重复技术,在最终的掩模版上产生具有一定行数和列数的重复图形阵列,这样,在将来制作的每一个硅片(Wafer)上将有若干个集成电路
33、芯片。通过这样的制版过程,就产生了若干块的集成电路分层掩模版。通常,一套掩模版有十几块分层掩模版。集成电路的加工过程的复杂程度和制作周期在很大程度上与掩模版的多少有关。2)光刻加工过程也成为图形转移工艺。通常,光刻次数越多,就意味着工艺越复杂。另方面,光刻所能加工的线条越细,意味着工艺线水平越高。光刻工艺是完成在整个硅片上进行开窗的工作。a. 涂胶 把光致抗蚀剂(光刻胶)涂覆在氧化膜上的过程称为涂胶。光刻胶受到特定波长光线的作用后,导致其化学结构发生变化,使光刻胶在某种特定溶液中的溶解特性改变。b. 曝光 在涂好光刻胶的硅片表面上覆盖掩模版,即将掩模置于光源与光刻胶之间,利用紫外光(或X射线、
34、离子束、电子束等)透过掩模对光刻胶进行选择性照射。在受到光照的地方,光刻胶发生光化学反应,从而改变了感光部分的胶的性质。曝光时准确的定位和严格控制曝光强度与时间是其关键。c. 显影与烘片 曝光后的光刻胶,其分子结构产生化学变化,在特定溶剂或水中的溶解度也不同,利用曝光区和非曝光区的这一差异,可在特定溶剂中把曝光图形呈现出来,这就是显影。有的光致抗蚀剂在显影干燥后,要进行高温处理,使它发生热聚合作用,以提高强度,叫做烘片。注:为保证质量,显影后的硅片要进行严格检查。d. 刻蚀 利用化学或物理方法,将没有光致抗蚀剂部分的氧化膜去除,称之为刻蚀。刻蚀的方法很多,有化学刻蚀、离子刻蚀、电解刻蚀等。虽然
35、,光刻和刻蚀是两个不同的加工工艺,但因为这两个工艺只有连续进行,才能完成真正意义上的图形转移。在工艺线上,这两个工艺是放在同一工序,因此,有时也将这两个工艺步骤统称为光刻。e. 剥膜与检查 用剥膜液去除光致抗蚀剂的处理为剥膜。剥膜后洗净修整,进行外观线条尺寸、间隔尺寸、断面形状、物理性能和电学特性等检查。3)选择型扩散(参考PPT)所谓热扩散掺杂就是利用原子在高温下的扩散运动,使杂质原子从浓度很高的杂质源向硅中扩散并形成一定的分布。热扩散通常分两个步骤进行:预淀积和再分布。预淀积是在高温下,利用杂质源,如硼源、磷源等,对硅片上的掺杂窗口进行扩散,在窗口处形成一层较薄但具有较高浓度的杂质层。这是
36、一种恒定表面源的扩散过程。再分布是利用预淀积所形成的表面杂质层做杂质源,在高温下将这层杂质向硅体内扩散的过程。通常再分布的时间较长,通过再分布,可以在硅衬底上形成一定的杂质分布和结深。再分布是限定表面源扩散过程。注:为加工新的一层电路,再次生长硅氧化物,然后沉积一层多晶硅,涂敷光刻胶、重复影印、蚀刻过程,得到含多晶硅和硅氧化物的沟槽结构。重复多遍,形成一个3D的结构,这才是最终的CPU的核心。每几层中间都要填上金属层作为导体。Intel的Pentium 4处理器有7层,而AMD的Athlon(速龙) 64则达到了9层。 金属层采用真空镀膜的方法。将导电性良好的金属(如铝、金)加热使之变成蒸气原
37、子飞溅到硅片表面,沉积一薄层金属膜的技术称为真空镀膜,可解决集成电路布线或引线的问题。所以,在图形转移工艺过程中,一般要对硅片进行10 多次光刻,其中包括对绝缘膜(SiO2膜、Si 3N4)、半导体膜(单晶Si、多晶Si)和导体膜(Al,Al-Si, W膜)的光刻,才能形成最终的图形。3.1.3 硅片测试经过上道工序,硅片上形成一个一个的小格,即晶粒。一般情况下,同一片晶圆上加工同一规格、品种的产品。用针测仪对每一个晶粒测试其电气特性。将不合格的晶粒标上标记。3.1.4 后半制程:包括封装和芯片测试将晶圆分开,分割成一个一个的晶粒。这时的CPU是一块块晶粒,它还不能直接被用户使用,必须将它封入
38、一个陶瓷的或塑料的封壳中,这样它就可以很容易地装在一块电路板上了。封装结构各有不同,但越高级的CPU封装也越复杂,新的封装往往能带来芯片电气性能和稳定性的提升,并能间接地为主频的提升提供坚实可靠的基础。这样,芯片完制作完成了。芯片加工的最后一道工序为测试。将封装后的芯片在各种环境下测试其电气特性,如消耗功率、运行速度等,根据其电气特性可划分为不同的等级。当然,最后要看一下整体良率是指通过最后测试的良好芯片(Good Chips)总数与用于生产之所有晶圆上的晶粒(Dies)总数的比值。整体良率决定一座IC芯片生产工厂是赔钱还是赚钱。至此,一块完成的芯片制作完成,即我们通常看到的黑色的或褐色的,四
39、边或两边带有许多插脚或引线的矩形小块。3、2 薄膜成形技术薄膜材料种类很多,根据不同使用目的可以是金属,半导体硅、锗、绝缘体玻璃,陶瓷等。从导电性考虑,可以是金属、半导体、绝缘体或超导体;从结构考虑,可以是单晶、多晶、非晶或超晶格材料;从化学组成来考虑可以是单质、化合物或无机材料、有机材料等。化学气相沉积是在容器中通以气相的、用以构成薄膜材料化学物质,使其在加热的基片表面进行高温化学反应,从而在基片上形成薄膜的技术。离子镀膜:将一定能量的离子束轰击某种材料制成的靶,离子将靶材粒子击出,使其镀覆到靶材附近的工件表面上。离子镀膜层的附着力强,镀层组织紧密。可镀各种金属、非金属、化合物、半导体。3、
40、3 光刻工艺由于电子质量极轻,在感光胶中的散射范围很大,这些散射电子会影响邻近电路图形的曝光质量,因而邻近效应很难控制。为了提高生产率和减小邻近效应,目前正在广泛研究限定角度投影电子束光刻技术。电子束光刻的主要缺点在于产出量,加工过程较慢,不能用于制造大多数集成电路。离子束曝光技术具有一些电子束无法比拟的优点,与电子相比,最轻的离子也要比电子重近2000倍。因此离子在感光胶中散射范围极小,邻近效应几乎为零。此外,由于离子质量重,在同样的能量下,感光胶对离子的灵敏度要比对电子高数百倍。缺点:离子束需要在真空下工作,硅片和掩模操作不方便;离子束是带电粒子,由于空间电荷作用使图形的清晰程度和图形位置
41、精度受限;离子束可使下层基底受损。3、4 掺杂技术离子注入:进入硅中的杂质离子在一定的位置形成一定的分布。通常,离子注入的深度(平均射程)较浅且浓度较大,必须重新使它们再分布。掺杂深度由注入杂质离子的能量和质量决定,掺杂浓度由注入杂质离子的数目(剂量)决定。 同时,由于高能粒子的撞击,导致硅结构的晶格发生损伤。为恢复晶格损伤,在离子注入后要进行退火处理,根据注入的杂质数量不同,退火温度在450950之间,掺杂浓度大则退火温度高,反之则低。在退火的同时,掺入的杂质同时向硅体内进行再分布,如果需要,还要进行后续的高温处理以获得所需的结深和分布。 离子注入技术以其掺杂浓度控制精确、位置准确等优点,正
42、在取代热扩散掺杂技术,成为VLSI工艺流程中掺杂的主要技术。 4、硅微细加工工艺微致动器又称微驱动器或微执行器,是能够产生和执行动作的一类微机械部件或器件的总称。比如微马达、微夹持器、微泵、微阀门、微闸门、微齿轮、微转轴等。4、1 硅体微加工技术硅的体微加工技术是指利用腐蚀工艺对块状硅进行准三维结构的微加工,以形成所需要的硅微结构,主要包括腐蚀和停止腐蚀两项关键技术。腐蚀又称蚀刻,是微加工中的重要工艺之一。它是指在需要的地方通过物理或化学的方法对原有材料的去除。物理腐蚀通常是指干法腐蚀(使用气体腐蚀剂),化学腐蚀则通常指湿法腐蚀(使用液体腐蚀剂)。蚀刻独立于光刻的重要的一类微细加工技术,但刻蚀
43、技术经常需要曝光技术形成特定的抗蚀剂膜,而光刻之后一般也要靠刻蚀得到基体上的微细图形或结构,所以刻蚀技术经常与光刻技术配对出现。以往的硅微细加工经常采用湿法刻蚀。(1)湿法腐蚀常用的湿法腐蚀方法主要有两种,即各向同性腐蚀和各向异性腐蚀。各向同性腐蚀是指腐蚀沿基底的各个方向以同一速率发生;而各向异性腐蚀则在优先的方向上以较快的速率腐蚀。1)各向同性腐蚀各向同性刻蚀是在任何方向上刻蚀速度均等的加工,可以制造任意横向几何形状的微形结构,高度一般仅为几微米。大多数化学刻蚀是不易控制的各向同性刻蚀。最大缺点就是在刻蚀图形时容易产生塌边现象,即在纵向刻蚀的同时,也出现侧向钻蚀,以至刻蚀图形的最小线宽受到限
44、制。通常,采用刻蚀系数来反映刻蚀向纵向深入和向侧向钻蚀的情况。侧向钻蚀越小,刻蚀系数越大,刻蚀部分的侧面就越陡,刻蚀图形的分辨率也就越高。但由于存在侧向钻蚀,这对于线宽在微米和亚微米量级的图形刻蚀来说是难以容忍的。微机械加工常用的刻蚀法各向异性刻蚀法。各问同性腐蚀剂在各个方向上的腐蚀速率几乎相同。由于反应中的扩散限制,腐蚀会在狭窄的通道内慢下来,在这种情况下,搅动腐蚀剂能够控制腐蚀速率和腐蚀结构的最终形状。通过适当的搅动腐蚀剂,能得到具有球形表面的坑和腔,甚至可以得到近乎完美的半球形,搅拌的作用是为了加速反应物和产物的转移,并保证转移在各个方向的一致性。通常制造微机械需要深度达几十个微米,深度
45、比较大能够形成三维空间结构的刻蚀技术,故多采用异向刻蚀技术。它是一种在特定方向上刻蚀速度大,其它方向上几乎不发生刻蚀的加工方法。2)各向异性腐蚀原理对于特定的腐蚀剂,如KOH,硅单晶不同晶面的腐蚀速度不同。一般对硅的(100)晶面的腐蚀速度最快,(110)晶面次之,(111)晶面的腐蚀速度最慢。即各向异性腐蚀与晶片的结晶取向密切相关。3)停蚀工艺重掺杂停蚀:硅的掺杂浓度和掺杂杂质种类对硅的腐蚀速度有很大影响。轻掺杂和重掺杂的腐蚀速度之比高达几百比一;采用重掺杂停蚀时,首先(100)硅在N型或P型硅表面通过扩散或外延的方法产生一层重掺杂P层;然后在硅片背面热生长Si02,用来制作掩膜;最后在掩膜
46、上刻蚀窗口,窗口边缘沿(010)晶轴方向,并在腐蚀剂中腐蚀,结果腐蚀到重掺杂层会停下来。 (111)面停蚀 : 目前常用的KOH系统等腐蚀剂对(100)和(111)面的腐蚀速率相差极大,因此如选用(111)面作为停蚀面,就可以在(100)面上腐蚀出(111)取向的硅膜。由于在(100)的硅片上不能直接生长(111)的硅,可利用热键合工艺将(100)与(111)硅“融合”在一起。图616是在(100)面上用Si02做掩膜形成腐蚀窗口,进行腐蚀,在(111)面停蚀,得到高精度的硅膜。在完成刻蚀后,要对工件进行充分水洗,以便把到蚀液全部除去。而后立即浸入剥膜液中,抗蚀剂一接触剥膜液就会很容易地分离或
47、溶解,用水洗可彻底清洗干净,然后用热风干燥。(2)干法腐蚀干法刻蚀是指利用一些高能束进行刻蚀。注:不需要大量的有毒化学试剂,不必清洗。比如离子束刻蚀和激光刻蚀。硅体微加工主要是通过光刻和化学刻蚀等在硅基体上得到一些坑、凸台、带平面的孔洞等微结构,它们成为建造悬臂梁、膜片、沟槽和其它结构单元的基础,最后利用这些结构单元可以研制出压力或加速度传感器等微型装置。4、2 硅表面微加工技术正当体加工成为加工微机械单元的强有力工具时,为适应微装置设计的多样性、灵活性以及器件功能逐步改善的需要,微细加工领域又诞生了许多新概念和新技术。1985年,牺牲层技术真正应用于微细加工方面,于是出现了表面微加工技术。注
48、:牺牲层技术工艺的目的是使结构薄膜与衬底材料分离,得到各种所需的可变形或可动的表面微结构。如图给出了牺牲层技术表面微加工的工艺步骤。(a)基础材料,一般为单晶硅晶片3(b)在基板上沉积一层绝缘层作为牺牲层;(c)在牺牲层上进行光刻,刻蚀出窗口;(d)在刻蚀出的窗口及牺牲层上沉积多晶硅或其他材料作为结构层;(e)从侧面将牺牲层材料腐蚀掉,释放结构层,得到所需微结构。通过在硅片表面沉积的牺牲层和结构层可以制作三维微结构。图626是需要两个牺牲层和两个结构层的中心销轴承的制作过程。(a)沉积第一层牺牲层,并制作与凸起点相匹配的凹坑(横截面图);(b)沉积第一层结构层,并制作转子图形,此时转子的凸起点
49、自动形成(横截面图);(c)沉积第二层牺牲层,并制作中心销轴承的指定区域(横截面图);(d)沉积第二层结构层,此时转子的中心已嵌入牺牲层,然后溶去牺牲层释放转子(横截面图)。表面微机械加工技术的主要优点是:充分利用了现有的IC生产工艺,对机械零部件尺度的控制与IC一样好,因此这种技术和IC完全兼容。堆装技术:如果由于某些复杂的微结构即使采用异向刻蚀工艺也很难制造,因此,可以利用刻蚀等工艺先制造出不同形状的平面结构,在把这些平面结构一层层组合连接起来,获得用一般方法无法制造的三微形状的微机械(如冷焊、黏结等)。 5、LIGA技术LIGA优势:(1)可以制造由各种金属材料如镍、铜、金、镣钻合金以及
50、塑料、玻璃、陶瓷等材料制成的微机械。因此,较硅材料的加工技术有了一个很大的飞跃。(2)由于同步辐射X射线具有很强的穿透力,因此可以制作具有很大纵横比的微结构。比如纵向尺寸可达数百微米,最小横向尺寸为1um的结构。尺寸精度达亚微米级而且有很高的垂直度,平行废和重复精度。(3)LIGA适合于制作平面图形复杂的三维结构。这一点是硅微细加工所不具备的。因为硅微细加工采用各向异性腐蚀,沿不用的晶轴方向溶解速度不一样,所以在硅晶体中生长的结构不可能是任意的。而用LIGA制作的微结构,其二维平面图形可任意设计,即掩膜图形可任意设计。(1)同步辐射X射线深层光刻注:被曝光过的抗蚀剂将被显影除去,所以该模扳即为
51、掩模覆盖下的为曝光部分的抗蚀剂层,它具有与掩模图形相同的平面几何图形。同步辐射X射线除具有普通x射线所具有的波长短、分辨率高、穿透力强等优点外,还具有特定的优点,主要包括:几乎是完全平行的x射线辐射,可进行大焦深(10 ym)的曝光,减小丁几何畸变的影响;高辐射强度,比普通x射线强度高两个数量级以上LIGA技术要求掩模的基底抗辐射能力强,稳定性好,掩模体厚。注:而且由于结合了模具生产的成形技术,LIGA为非半导体材料微结构的廉价生产提供了可能,具有批量生产的特性。LIGA技术应用:LIGA技术自诞生以来就一直被认为是进行微三维立体构件加工的最有力的手段之一。目前,欧、美、日等国已开始运用LIG
52、A技术进行批量生产微构件商品。由于微小齿轮的结构相对简单,而且应用面极广,因此德国、美国等科学家在进行LIGA技术的基础研究时大多从微齿轮的制作开始。目前已可制作出能够相互啮合的渐开线齿形的齿轮。研究表明,LI GA技术可以自由地进行二维设计,并且在设计时能够进行计算机优化,精确度可以达到亚微米级。威斯康星-麦迪逊大学通过LIGA方法制作的微齿轮和组装后的微马达。(d)LIGA工艺得到的三个镍材料的微型齿轮,每个齿轮高100mm(e)组装后的电磁驱动微马达的STM 照片,由牺牲层和LIGA技术获得,转子直径为150mm,三个齿轮的直径分别为77mm,100mm和150mm。作为一种实用的微细加
53、工手段,LIGA工艺的一大突出特性就是可以完成大纵横比微结构的制作。图719是日本学者用LIGA技术完成的部分微结构制作。其中图719(a)是制作的Ni金属模具,它的高度为15um,线宽为02um,纵横比为75;(b)为Ni金属模具,它的高度为200um,线宽为2um,纵横比为100;上为厚度为200um的微结构图片。微传感器和微致动器的性能很大程度上取决于其敏感器件的灵敏度,而敏感器件则大多为大纵横比的微悬臂结构,这正是LIGA技术的加工特长。图720是德国学者用LIGA技术制作的部分微传感器和微致动器结构。可以看出应用LIGA技术已经能够制作除结构相当复杂的微系统结构。微细电火花加工技术在
54、金属材料的微细加工中发挥了重要作用,但微细电极,尤其是微小成型电极的制备却相当困难,一直是制约该技术广泛应用的瓶颈问题。由于LIGA技术的批生产特性,可以用其制作复杂形状金属成形电极,从而大大拓宽微细电火花加工技术的加工能力和应用领域。将两种或两种以上的微细加工技术进行有效的集成,充分发挥各自的技术特点,将是未来微细加工技术发展的必然趋势之一。 图724是日本学者用LICA技术制作出电火花加工用的微细成形电极,然后再用制作出的电极进行微细电火花加工实例。由于在加工衬底上一次制作出的是一批电极,因此,用此电极一次就可以加工出一批工件。图724(a)、(b)是用此方法制作出的2020的圆柱电极阵列
55、以及用此电极在厚为50um的不锈钢片上加工出的微细阵列孔,每根电极的直径为20um,材料为钢,加工后孔的直径为30-32um之间;图724(c)、(d)是用此方法制作出的成形电极以及用此成形电极加工出的工件照片。6、纳米加工技术纳米科技(NST,Nano Science & Technology)是一门在0.1100 nm的尺度空间内研究电子、原子和分子等的结构特性、运动规律和相互作用的崭新学科,它是现代物理(介观物理、量子力学、混浊物理)和先进技术(微电子、计算机、扫描隧道显微技术)相结合的产物,并由此派生出一系列的新兴学科。纳米是英文nano的译名,是一种长度单位,原称毫微米,就是10的- xingkong星空体育
56、9次方米(10亿分之一米)。纳米结构通常是指尺寸在100纳米以下的微小结构。从具体的物质说来,人们往往用细如发丝来形容纤细的东西,其实人的头发一般直径为20-50微米,并不细。假设一根头发的直径为0.05毫米,把它径向平均剖成5万根,每根的厚度即约为1纳米。单个细菌用肉眼看不出来,用显微镜测出直径为5微米,也不算细。极而言之,1纳米大体上相当于4个原子的直径。NST产生的源头可以追溯到20世纪50年代,当时一位著名的物理学家 (诺贝尔奖获得者)曾经提出:逐级缩小生产装置,以至最后由人类直接按照所需来排布原子,制造产品。这在当时还只是一个美好的梦想。1977年麻省理工学院的德雷克斯勒认为,上述想
57、法可以从模拟活细胞中生物分子的人工类似物分子装置开始,并命名为纳米技术。纳米科技是在20世纪80年代末90年代初逐步发展起来的前沿性、交叉性新兴学科领域。“纳米技术”已经成为当今世界的标志性词组之一,纳米技术几乎已经深入到当代社会生活的所有领域。(可补充:纳米技术包含下列四个主要方面,主要讲纳米材料:(1)纳米材料:当物质到纳米尺度以后,大约是在0.1100纳米这个范围空间,物质的性能就会发生突变,出现特殊性能。这种既具不同于原来组成的原子、分子,也不同于宏观的物质的特殊性能构成的材料,即为纳米材料。如果仅仅是尺度达到纳米,而没有特殊性能的材料,也不能叫纳米材料。过去,人们只注意原子、分子或者宇宙空间,常常忽略这个中间领域,而这个领域实际上大量存在于自然界,只是以前没有认识到这个尺度范围的性能。第一个真正认识到它的性能是日本科学家,他们在20世纪70年代用蒸发法制备超微离子,并通过研究它的性能发现:一个导电、导热的铜、银导体做成纳米尺度以后,它就失去原来的性质,表现出既不导电、也不导热。磁性材料也是如此,象铁钴合金,把它做成大约2030纳米大小,磁畴就变成单磁畴,它的磁性要比原来高1000倍。80年代中期,人们就正式把这类材料命名为纳米材料。为什么磁畴变成单磁畴,磁性要比原来提高1000倍呢?这是因为,磁畴中的单个原子排列的并不是很 xingkong星空体育
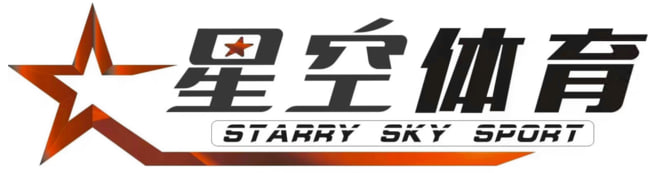
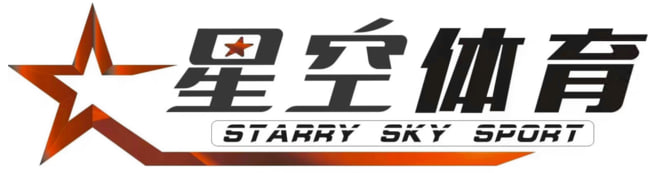
同类文章排行
- xingkong星空体育:先进制作技术范
- 王健林又悄悄卖了几家万达广场!保险、信托
- 为什么互联网产品越来越难做了?
- 国产顶级“二次元”IP:三国
- 在人工智能炒热机器人时,也被人把风带进了
- 珍爱智商,远离“区块链”
- 刮着大风的人工智能,躺着赚钱的自动驾驶
- 共享,正从风口到风险
- 智能音箱,正走在智能手表的老路上
- AI在内容分发上的绊脚石
最新资讯文章
- 星空体育:工艺技术论文范文10篇
- 星空体育:【深度】21世纪中国现代机械制
- 星空体育:食品机械的发展历程分为哪几个阶
- 星空体育:解读:现代超精密加工技术的发展
- 星空体育:现代机械加工的发展趋势
- 星空体育:机器人导论知识点总结
- 星空体育:数控技术就业前景及就业方向分析
- 星空体育:机械制造自动化论文十篇
- 星空体育:现代机械加工技术的发展探究论文
- 星空体育:农机产品质量为何难以提高?5大
- 星空体育:2023-2028年中国数控机
- 星空体育:现代制造技术的发展十篇
- 星空体育:浅谈现代机械制造技术发展与趋势
- 星空体育:生产实习报告心得体会
- 星空体育:汽车新材料的应用及发展趋势
- 星空体育:机械制造的技术特点及未来发展探
- 星空体育:机械制造技术及发展趋势
- 星空体育:机械面试常见问题
- 星空体育:信息技术发展规划十篇
- 星空体育:深孔钻镗床的知识简介运用范围及